2025-4-18
倉庫のピッキング作業にタブレット導入!在庫管理のデジタル化で残業ゼロ達成
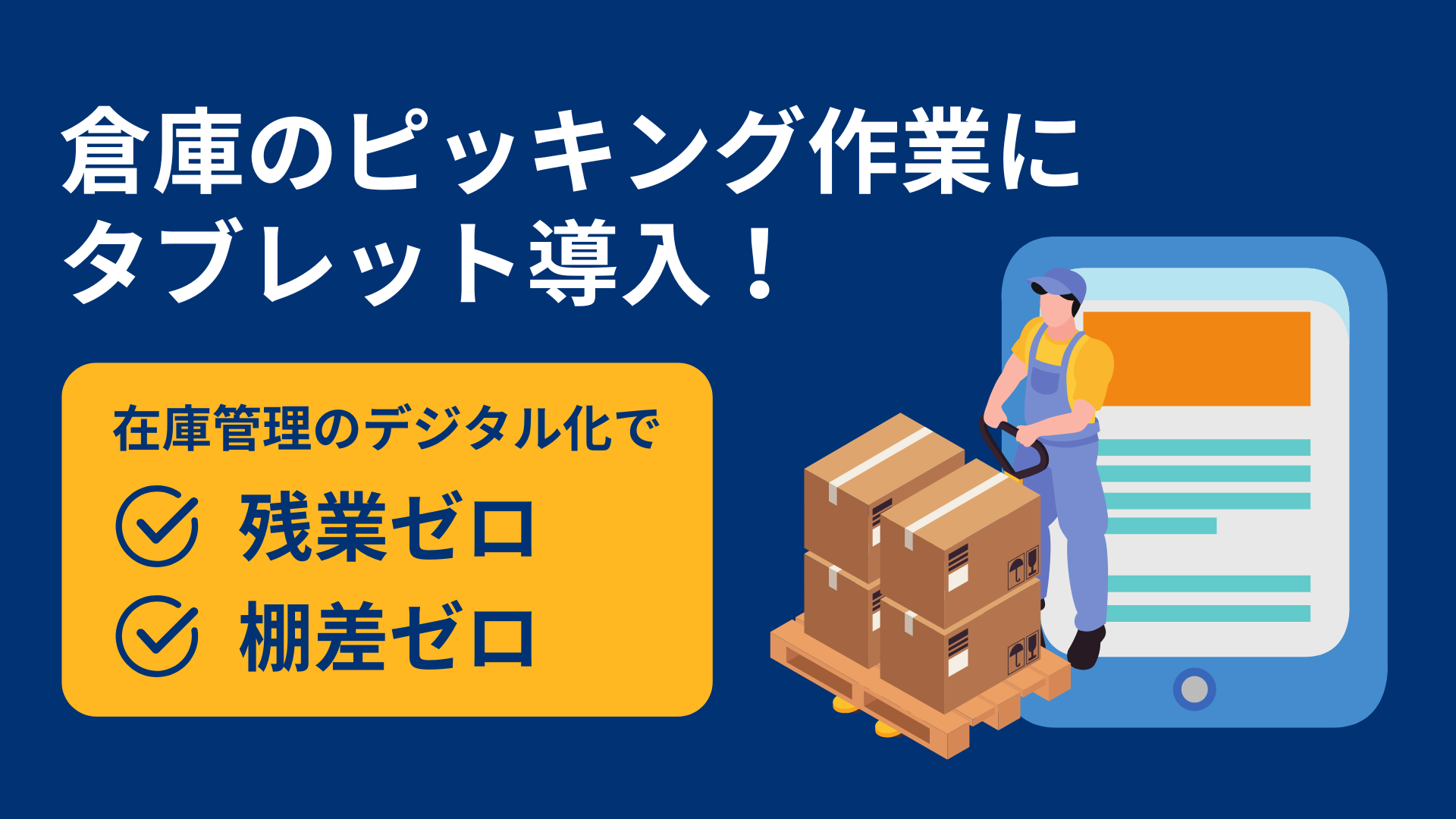
- 業界
-
製造業
- 事業内容
-
製造および販売
- 従業員数
-
100-500人
- 売り上げ規模
-
100億円以上
開発概要
これまで紙で行っていたピッキング作業を、タブレット端末(iPad)で行えるシステムを開発しました。これにより倉庫内のデジタル化ができ、出荷作業と棚卸作業が効率化、残業ゼロを達成することができました。
こんなピッキングシステムを開発しました
- 当日の出荷に関するピッキング指示がタブレット画面に表示される
- 作業者はこの指示に従って製品をピッキングする
- 該当製品のQRコードを読み取ることで、在庫の消込が自動で行われる
タブレットピッキングシステムの開発ポイント
手入力不要!基幹システムより自動的にデータを出力
表示する出荷データは、基幹システムに登録されている最新の出荷データが、自動的にタブレットのピッキング画面に反映される仕組みです。手作業で出荷情報を入力したり、別のシステムからエクスポートしたりする手間はありません。
1日に何度もデータの取り込みが可能
出荷の追加やキャンセルが発生する場合も考慮して、一日に何度もデータの取り込みが可能なよう開発しました。
必要な情報が一元的に表示
トラック情報と出荷先もデータに連携させ、担当者が荷揃えに必要なピッキング情報をまとめて表示できるようにしました。例えば、特定のトラックに積み込む荷物を担当する作業者は、そのトラックに関連するすべての出荷先の製品リストを一度に見ることができるため、効率的に荷物を集めることができます。
複数の情報源を確認したり、紙のリストを照らし合わせたりする手間が省けたことで、ピッキング作業の効率化、時間の短縮、ミスの削減が期待されます。
在庫データ、差異の発生原因も特定可能
年に2回行われる棚卸作業においては、QRコードリーダーで読み取ったデータと、管理している実在庫データを突き合わせ、過不足がすぐに分かるようにしました。
差異があった場合には出庫・入庫でのスキャン実績とロケーション管理をすることにより、トレースされたデータを追えるようにしました。その結果、差異の発生原因を特定することが可能になりました。
システムの構成要素
- iPadアプリケーション(Objective-C)
- QRコードリーダーのプログラム開発(C#.net)
- Windowsアプリケーション(C#.net)
- 管理サーバ(Java)
導入の背景
出荷量の増加に伴い、紙ベースの業務プロセスに限界が訪れた
こちらの企業では、毎朝その日の出荷データを紙に印刷し、複数のピッキング担当者に配布するという倉庫運用を行っていました。
しかし、日々の業務では出荷情報の追加やキャンセルが頻繁に発生しており、このような変更が生じるたびに、新たな情報を印刷し、広い倉庫内にいる複数のピッキング担当者のもとへ再度届けなければならないという煩雑な作業が発生していました。紙での情報伝達は、どうしても時間と手間がかかってしまい、事務方と現場双方にとって大きな負担となっていたのです。
年々の出荷量増加により問題はさらに深刻化、残業も増えました。時間内に作業を終えることが困難になっていった結果、トラックを待たせてしまうといった物流上の問題も発生してしまったそうです。
ピッキング作業者を増やしても、根本的な業務プロセスが紙ベースである限り、効率化には限界があることから、今回ご相談を頂きました。
導入の決め手
倉庫のピッキングにタブレットを使いたい!
システム導入を検討する際、多くのお客様は現状の運用を大きく変えることを避けたがる傾向があり、表面的な課題解決を求めることが多いです。例えば「もっと早く印刷できるプリンタはないか」「追加やキャンセルをコントロールできる部分的なシステム化をしたい」「出荷量を平準化できる仕組みを構築したい」等です。ですがこれらは、根本的な課題である紙ベースの運用による非効率性や情報伝達の遅延を解決するものではありません。
しかし、今回のお客様は「無線設備でタブレット端末を活用したい」という明確なテーマをご提示されました。このご要望は、従来の紙媒体に代わるデジタルな情報活用を目指すものであり、印刷という工程を極力減らしたピッキングシステムの構築という提案につながりました。
システム導入を考える際、データを連携することは非常に重要です。一旦データ連携が切れてしまうと手間だけでは無く、ミスも多くなります。これまでは紙に印刷するという工程があることで、基幹システムからのデータ連携を阻害していましたが、お客様の先進的な意向と、ペーパーレスへの早期理解があったからこそ、スムーズに開発させていただくことができました。
スクラッチ開発で、ニーズを満たすシステムの提供
以下お客様のニーズをすべて満たすシステムをご提案し、導入の決め手としてご評価いただきました。
お客様の課題を丁寧にヒアリングすることで、見えてくることがあります。既存パッケージではなく、スクラッチ開発に強い当社だからこそ、痒い所に手が届くべストなシステムを開発することができました。
残業を削減したい
タブレット端末の導入で紙による情報伝達の遅れや印刷の手間がなくり、ピッキング作業が迅速化します。結果として残業時間の削減につながることが期待されました。
庫内の整理整頓
基幹システムの最新データと連携することにより、リアルタイムな在庫管理とロケーション管理が可能になります。そうすることで倉庫内の物の流れが明確になり、整理整頓が進むと考えられました。
不慣れな作業者への対応
タブレット画面にピッキング指示が表示され、QRコードリーダーで消込を行うシンプルな操作性は、ピッキングの経験の浅い、またデジタルツールに不慣れな作業者でも容易に業務に取り組めることが期待されました。
導入後の効果
残業ゼロを実現
急に紙がなくなることで、一時的に現場に混乱が生じる可能性はありましたが、紙もシステムも両方使える状態にはあえてしないということでお客様にはご承知いただきました。段階的な導入ではなく、やるしかない環境を作り出すという決断も、システムへの早期適応を促す重要な要素だと当社は考えています。
裏では万が一のトラブル対応用として印刷機も準備しておりましたが、使うこともなく、おお客様は日を追うごとにシステム慣れして、一カ月もたたないうちに残業ゼロを達成することができました。
棚差ゼロも実現
業務効率化によって生まれた余裕は、単に残業時間の削減に留まらず、倉庫内の整理整頓という改善活動にも波及しました。先入先出(FIFO)に基づいた入出庫の運用が可能になったことは、製品の品質管理や陳腐化防止に繋がり、倉庫全体の効率性を高める上で重要な進歩です。
さらに、ロケーション管理を正しく行うことで、どの製品がどこに保管されているかがシステム上で正確に把握できるようになり、ピッキング作業の効率化や誤出荷の防止に大きく貢献し、システムの効果を最大限に引き出すことが可能になりました。
倉庫内の運用が正しく機能している証として挙げられているのが、数万点に及ぶ在庫に対する棚卸での棚差がゼロという驚異的な成果です。これは、日々の入出庫作業におけるQRコードリーダーによる正確なデータ入力と、システムによる実在庫データの厳密な管理・照合によって実現されています。もし差異が発生した場合でも、出庫・入庫のスキャン実績とロケーション管理のデータを遡ることで原因を特定できる仕組みが構築されているので、問題の再発防止にも繋がります。
年に2回行われる棚卸作業において、これだけの在庫数で棚差が全く発生しないということは、システムの導入が在庫管理の精度を飛躍的に向上させたことを示しており、倉庫運営の信頼性を大きく高める結果となりました。
倉庫システムのデジタル化と未来
デジタル化により現場主導の業務改善が活発化
システムは、一度構築したら終わりではなく、その後の現場の状況や要望に合わせて改修・改善を重ねていくことが非常に重要です。
今回のケースでも、業務のデジタル化によって現場の意識が変わり、デジタル技術への理解が深まった結果、現場主導でさらなる業務効率化を目指す動きが活発になりました。具体的には、「より便利に、より広範囲に、より連携したい」といったご要望が出され、システムの改修を重ねていきました。
VR、ドローン、AIがもたらす倉庫革命
そして、今後の倉庫システムの発展については、VR(仮想現実)、ドローン、ロボット、自動倉庫、AI(人工知能)といった新しい技術の活用が期待されています。
- VR
作業者のトレーニングや倉庫レイアウトのシミュレーションなどに活用できる可能性があります
- ドローン
広大な倉庫内での棚卸や在庫管理、セキュリティ監視などに役立つかもしれません
-
ロボット・自動倉庫
ピッキングや搬送作業の自動化を進め、省人化や効率化など、今後少子高齢化が進む日本に大きく貢献すると考えられます
-
AI
過去のデータ分析に基づいた需要予測や在庫最適化、作業スケジューリングの自動化など、より高度な倉庫運営を支援する可能性があります
当社は、倉庫システムの今後の発展には、保守的な姿勢を捨て、変化を恐れずに新しい技術を積極的に取り入れる決意を持つことが最も重要であると考えています。なぜなら、そうした姿勢こそが倉庫システムの未来を切り開く鍵となるからです。
この信念に基づき、当社はお客様に対して、有益な最新技術に関する情報を提供し、お客様の状況に寄り添った最適なご提案をすることをお約束します。